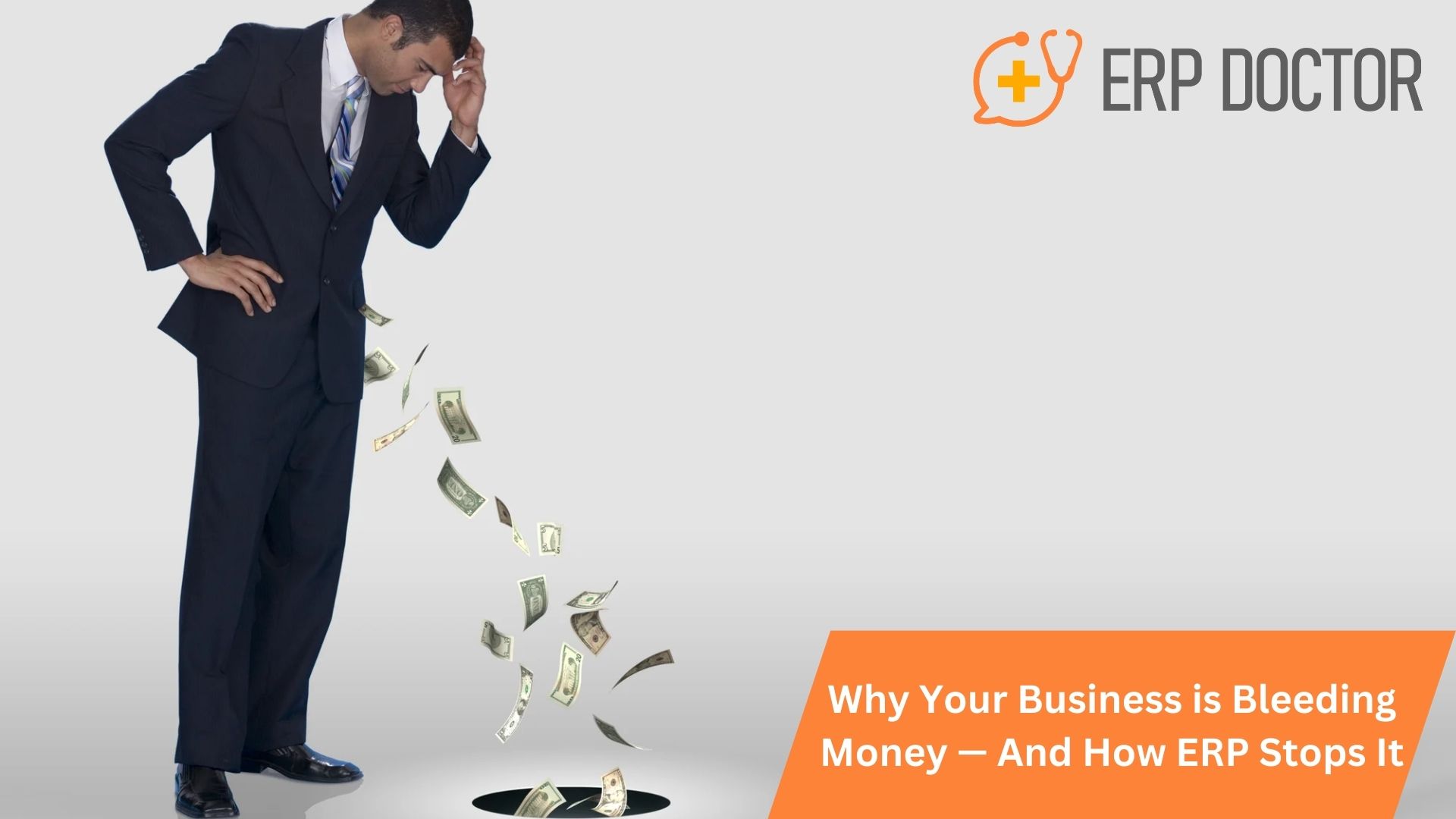
Why Your Business is Bleeding Money — And How ERP Stops It

Is Your Business Losing Money Without You Realizing It?
Running a business isn’t easy — and losing money without knowing where or why it’s happening makes it even harder. Many businesses experience financial drain through hidden inefficiencies, operational errors, and poor resource management. The frustrating part? Most business owners don’t even realize where the money is leaking from until it’s too late.
Common signs of financial leakage include:
- Overlapping and redundant processes.
- Mismanaged inventory leading to stockouts or overstocking.
- Inaccurate financial reporting.
- High operational costs due to manual tasks.
- Poor customer retention caused by inconsistent service.
This is where ERP (Enterprise Resource Planning) systems come into play. An ERP system integrates all your business processes — from sales and inventory to finance and customer service — into one platform. This centralization eliminates inefficiencies, automates manual tasks, and provides real-time data, helping you plug financial leaks and improve profitability.
In this article, we’ll explore how your business might be losing money — and how an ERP system can help you stop it, recover lost revenue, and improve business efficiency.
🚨 How Your Business is Bleeding Money
Financial leakage is a silent killer for businesses. If you’re not monitoring every aspect of your business in real time, you’re likely missing key areas where money is being wasted. Let’s take a closer look at the most common ways businesses lose money — and why an ERP solution is the key to fixing them.
✅ 1. Poor Inventory Management
Holding excess stock increases storage costs, while stockouts cause missed sales opportunities and dissatisfied customers. Businesses that rely on spreadsheets or disconnected systems for inventory management often face these issues.
Solution: A retail company frequently overstocked products due to poor demand forecasting. After implementing an ERP system, real-time inventory tracking allowed them to reduce excess stock by 30% and increase order fulfillment rates by 25%.
✅ 2. Inefficient Production Scheduling
Without proper visibility into supply chains and production schedules, businesses often waste resources on overtime, last-minute orders, and equipment downtime.
Solution: A manufacturing company suffered from inconsistent production cycles, leading to high labor costs and delayed orders. An ERP system enabled them to align production schedules with demand forecasts, reducing production costs by 20%.
✅ 3. High Labor Costs Due to Manual Processes
Manual data entry, order processing, and customer service are time-consuming and error-prone. Businesses that rely on manual work often experience higher operational costs and slower response times.
Solution: A logistics company automated order processing and invoicing using an ERP system. This reduced labor costs by 15% and increased order accuracy by 98%.
✅ 4. Financial Reporting Errors and Delayed Insights
Inaccurate financial reporting makes it difficult to track profitability and adjust business strategies. Businesses that rely on manual reporting or outdated systems often struggle to identify trends and make informed decisions.
Solution: A healthcare company streamlined its financial reporting with an ERP system, reducing reporting errors by 40% and speeding up month-end close by 30%.
✅ 5. Lack of Visibility into Profit Margins
Without a clear understanding of your business’s profit margins, it’s impossible to identify which products or services are most profitable. An ERP system provides real-time profit analysis at a granular level.
Solution: A technology company used ERP profit-tracking tools to identify high-margin products and focus marketing efforts on them, increasing profit margins by 15%.
✅ 6. Lost Sales Due to Poor Customer Experience
Inconsistent order processing, delayed deliveries, and poor customer service lead to lost sales and lower customer retention rates. An ERP system ensures all customer interactions are tracked and managed efficiently.
Solution: A food delivery company used ERP-driven order tracking and automated customer service to improve on-time delivery rates by 20%, boosting repeat orders by 25%.
✅ 7. Unnecessary Spending on Duplicate Software and Services
Many businesses use separate tools for accounting, inventory, and sales — leading to overlapping costs and integration issues. An ERP system consolidates all these functions into one platform, eliminating redundancy.
Solution: A retail company reduced software costs by 30% by consolidating all business operations under a single ERP platform.
✅ 8. Poor Cash Flow Management
Delayed invoicing, missed payments, and poor tracking of receivables affect cash flow. An ERP system automates billing and payment tracking to keep cash flow healthy.
Solution: A construction company automated billing and collections using an ERP system, improving cash flow by 18% and reducing late payments by 22%.
✅ 9. Inaccurate Demand Forecasting
Without reliable demand forecasts, businesses either overproduce (leading to wasted resources) or underproduce (leading to stockouts). An ERP system uses AI-driven forecasting to improve accuracy.
Solution: A manufacturing company increased demand forecast accuracy by 25% after switching to an ERP-based forecasting model.
✅ 10. High Operational Costs from Inefficient Workflows
When departments work in isolation, processes become slower and more expensive. An ERP system connects all departments, streamlining workflows and reducing costs.
Solution: A healthcare provider reduced operational costs by 12% after implementing an ERP system that integrated scheduling, billing, and patient records.
🔥 How ERP Stops the Financial Bleeding
An ERP system serves as the central nervous system of your business, providing real-time visibility into every aspect of your operations. Here’s how it helps prevent financial leakage:
✅ Automates repetitive tasks to reduce labor costs.
✅ Provides real-time insights into financial performance.
✅ Improves inventory accuracy and prevents overstocking.
✅ Increases production efficiency by aligning output with demand.
✅ Centralizes data to reduce software and service duplication.
✅ Enhances customer experience with faster order processing.
🔎 Ready to Stop Losing Money? Let ERP Fix It!
You don’t have to keep losing money to inefficiencies, poor tracking, and missed opportunities. An ERP system centralizes your data, automates processes, and provides real-time insights to improve business performance.
If your business is bleeding money, it’s time to stop the drain and start building profitability with ERP.
👉 Discover how ERP can transform your business — Schedule a demo today!
🧠 FAQs
1. How does ERP improve cash flow management?
ERP systems automate invoicing, track payments, and provide real-time cash flow insights, helping businesses manage working capital more effectively.
2. Can ERP help reduce labor costs?
Yes, ERP automates repetitive tasks and improves workflow efficiency, reducing the need for manual labor.
3. How does ERP help with inventory management?
ERP provides real-time inventory tracking and demand forecasting, helping businesses avoid overstocking and stockouts.
4. What types of businesses benefit most from ERP systems?
ERP systems benefit businesses in manufacturing, retail, healthcare, logistics, and service industries by improving operational efficiency.
5. Can ERP improve customer satisfaction?
Yes, ERP systems improve order tracking, response times, and customer service, leading to higher customer retention rates.
6. How does ERP reduce software costs?
ERP consolidates multiple business functions into a single platform, eliminating the need for separate tools and reducing licensing costs.
7. Is ERP suitable for small businesses?
Yes, ERP solutions are scalable, making them suitable for businesses of all sizes.
8. How does ERP improve decision-making?
ERP systems provide real-time insights and predictive analytics, helping businesses make informed decisions.
9. Can ERP improve supply chain visibility?
Yes, ERP systems provide end-to-end visibility into supply chains, improving production planning and delivery times.
10. How long does it take to implement an ERP system?
Implementation timelines vary, but most businesses can start seeing results within 2–6 months, depending on complexity.