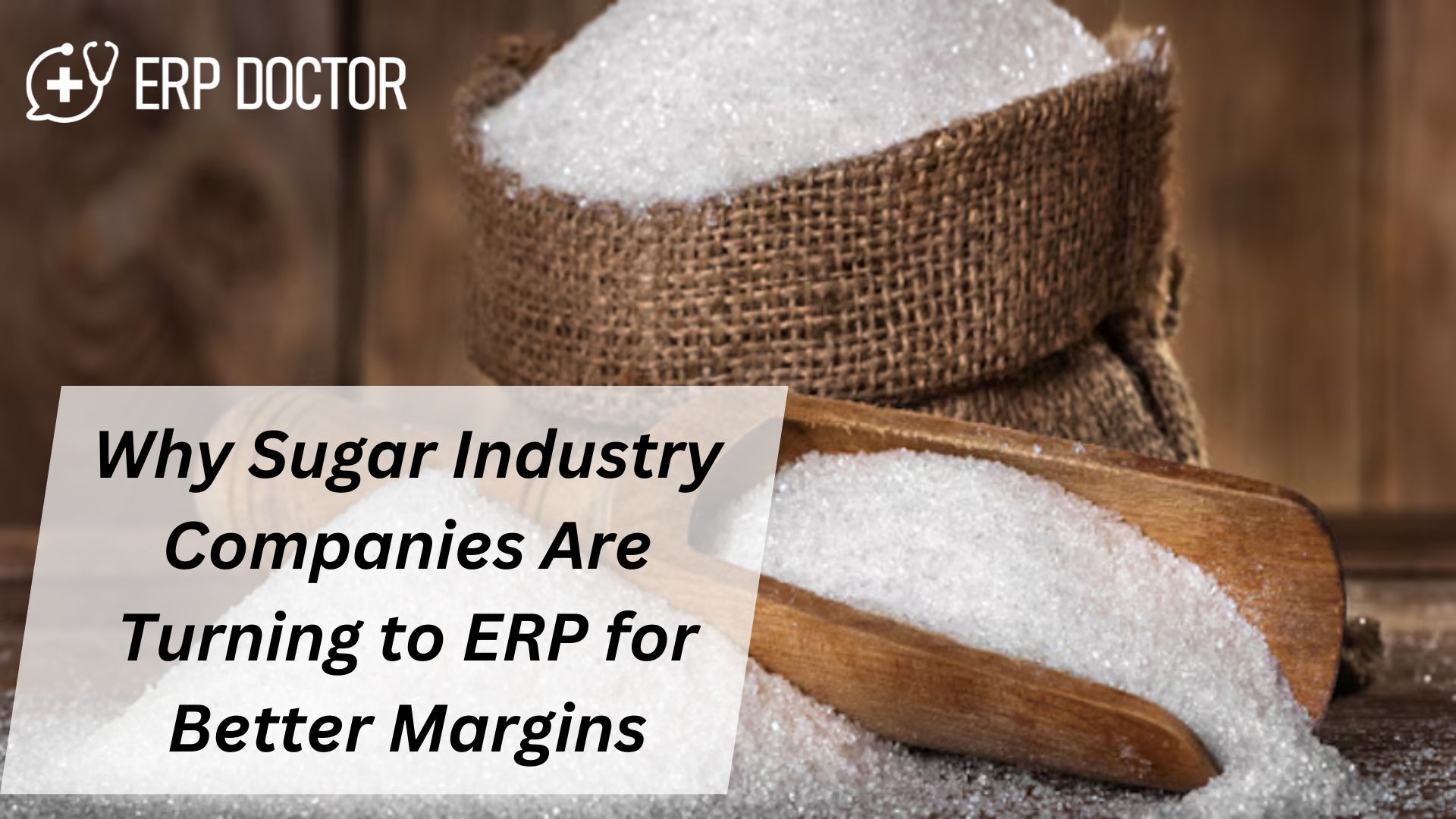
Why Sugar Industry Companies Are Turning to ERP for Better Margins
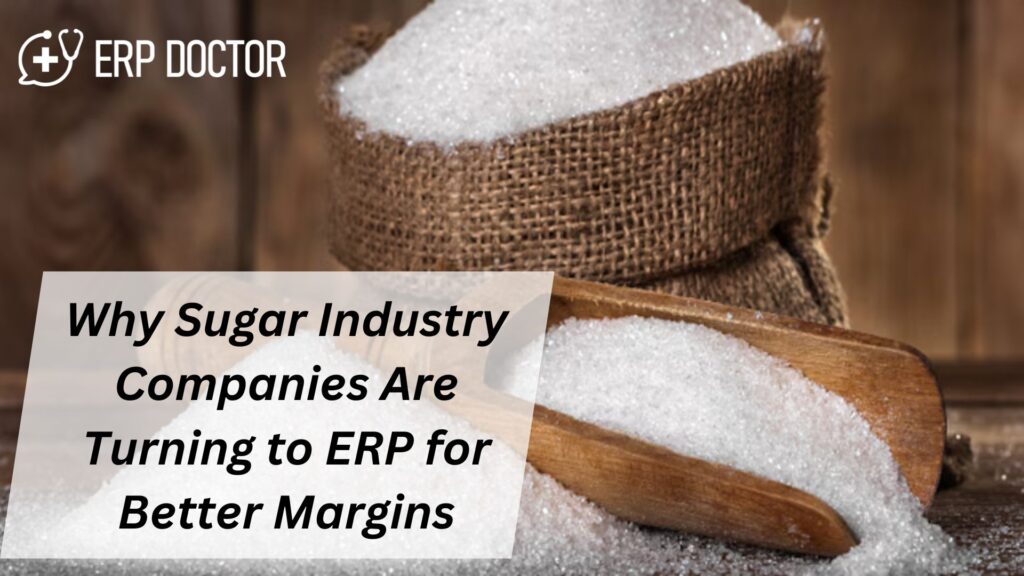
Sugar Industry Profitability Unlocked: The Impact of ERP Solutions
In today’s competitive market, sugar industry companies face mounting pressure to improve profitability, streamline production, and maintain high product quality. Managing complex supply chains, fluctuating raw material costs, and strict regulatory requirements pose significant challenges. To overcome these hurdles and improve operational efficiency, many sugar industry companies are turning to ERP (Enterprise Resource Planning) solutions.
Understanding the Challenges in Sugar Industry
The sugar industry is highly sensitive to various factors such as climate conditions, fluctuating global sugar prices, and changing government policies. Some of the key challenges include:
- Supply Chain Inefficiencies – Managing procurement, transportation, and storage of sugarcane or raw sugar.
- Cost Fluctuations – Constant changes in sugar prices and raw material costs.
- Production Complexities – Handling by-products, waste management, and optimizing production cycles.
- Quality Control – Ensuring product quality and consistency across batches.
- Regulatory Compliance – Meeting environmental and food safety standards.
Implementing an ERP system can address these pain points and help sugar companies improve their margins.
How ERP for Sugar Industry Improves Profitability
1. Enhanced Supply Chain Management
ERP software provides real-time visibility into the supply chain, helping sugar companies monitor procurement, inventory, and logistics. This ensures better coordination between farmers, suppliers, and processing plants, reducing delays and waste.
2. Improved Production Efficiency
ERP solutions for sugar industry companies automate production processes, optimize resource allocation, and minimize downtime. By integrating production data with inventory and quality control, companies can increase output while reducing costs.
3. Better Cost Control and Budgeting
ERP systems track costs at every stage of production and provide insights into cost-saving opportunities. With real-time cost monitoring, sugar companies can adjust pricing strategies and improve profitability.
4. Compliance and Quality Management
An ERP system ensures that sugar production meets industry standards and government regulations. Automated reporting, real-time tracking, and quality checks help maintain product consistency and avoid penalties.
5. Data-Driven Decision Making
With integrated data from procurement, production, sales, and distribution, ERP solutions provide actionable insights. Business leaders can make informed decisions based on market trends, demand forecasts, and performance metrics.
Key Features of ERP Implementation for Sugar Industry
- Inventory and Raw Material Tracking – Real-time tracking of sugarcane supply, storage, and production cycles.
- Automated Production Planning – Optimize batch production, resource allocation, and maintenance schedules.
- Financial Management – Manage costs, revenue, and profit margins with accurate reporting.
- Traceability and Compliance – Ensure complete product traceability and meet regulatory requirements.
- Sales and Distribution – Manage order fulfillment, customer relationships, and logistics from a centralized system.
Why SAP Solutions for Sugar Industry Stand Out
Leading ERP providers like SAP offer industry-specific solutions for sugar companies. SAP S/4 HANA and SAP Business One enable sugar manufacturers to integrate production, finance, and supply chain operations under a single platform. With SAP solutions, sugar companies benefit from:
✅ Real-time operational visibility
✅ Predictive analytics for better demand planning
✅ Automated compliance reporting
✅ Reduced production costs through process optimization
FAQs: How ERP is Boosting Margins in the Sugar Industry
1. What is ERP for the sugar industry?
ERP (Enterprise Resource Planning) for the sugar industry is a software solution that helps sugar companies manage production, supply chain, inventory, finance, and compliance from a single platform.
2. How can ERP improve profit margins in the sugar industry?
ERP helps reduce costs by automating processes, improving supply chain efficiency, and providing real-time data for better decision-making, which leads to higher profit margins.
3. What are the key challenges in the sugar industry that ERP solves?
ERP addresses supply chain delays, fluctuating raw material costs, production inefficiencies, quality control issues, and regulatory compliance.
4. How does ERP help with supply chain management in the sugar industry?
ERP provides real-time visibility into procurement, transportation, and inventory, helping companies avoid delays and reduce wastage.
5. Can ERP help with production planning in the sugar industry?
Yes, ERP automates production scheduling, optimizes resource use, and reduces downtime to improve overall efficiency.
6. How does ERP improve cost management in sugar manufacturing?
ERP tracks costs at every stage of production and provides insights into areas where expenses can be reduced or optimized.
7. What are the benefits of SAP solutions for the sugar industry?
SAP solutions provide real-time data, predictive analytics, automated reporting, and improved compliance, helping sugar companies increase efficiency and profitability.
8. How does ERP help with quality control in sugar manufacturing?
ERP tracks production data and automates quality checks to ensure consistency and meet industry standards.
9. Is ERP suitable for both large and small sugar companies?
Yes, ERP solutions like SAP Business One are scalable and customizable to meet the needs of both large manufacturers and small producers.
10. How long does it take to implement an ERP system for a sugar company?
Implementation time varies based on company size and complexity, but most ERP projects are completed within 3 to 6 months.
As sugar industry companies face increasing cost pressures and market volatility, ERP implementation provides a strategic advantage. By automating key business processes, improving supply chain efficiency, and enabling data-driven decision-making, ERP systems help sugar companies achieve better margins and sustained growth. SAP solutions for sugar industry offer tailored capabilities to meet the sector’s unique challenges, driving profitability and operational excellence.
Investing in an ERP system is no longer an option—it’s a necessity for sugar industry companies looking to stay competitive and maximize their margins.