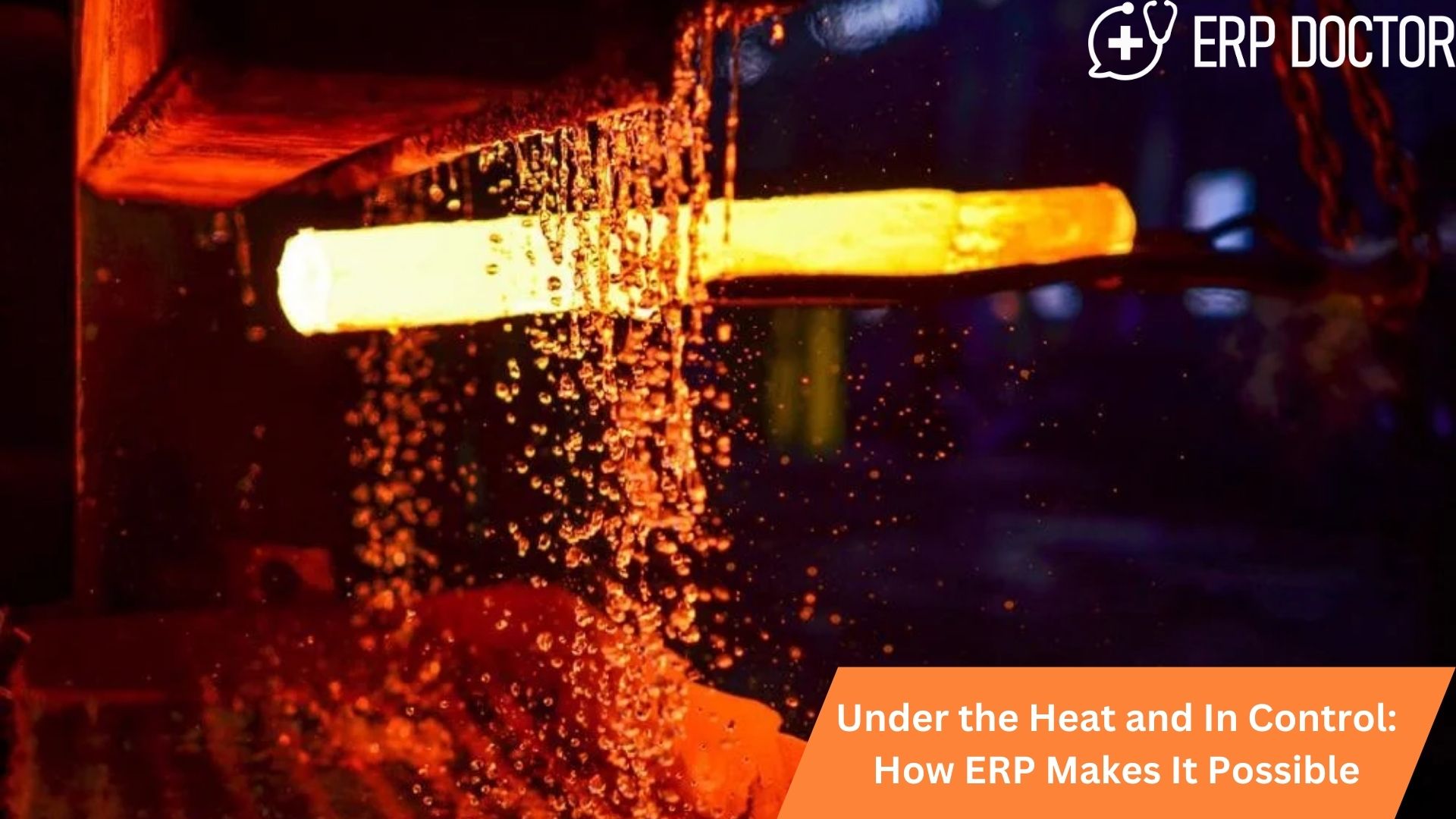
Under the Heat and In Control: How ERP Makes It Possible

How ERP Transforms Heat Treating Services with Precision and Efficiency
Heat treating is a complex and highly specialized process that requires precision, consistency, and strict quality control. Industries like automotive, aerospace, manufacturing, and metal fabrication rely heavily on heat treating to enhance the strength, hardness, and durability of metal components. However, managing heat treating services involves juggling multiple variables—temperature, timing, material composition, and equipment maintenance—all while adhering to industry regulations and maintaining cost efficiency.
This is where ERP (Enterprise Resource Planning) systems come into play. ERP solutions provide heat treating companies with a centralized platform to manage operations, automate scheduling, track inventory, ensure quality control, and streamline compliance. With real-time insights and automated reporting, ERP helps heat treating services operate more efficiently, reduce downtime, and improve profitability.
In this blog, we’ll explore the unique challenges of heat treating services and how ERP solves them, ensuring greater operational control and better business outcomes.
Challenges in Heat Treating Services
Heat treating is not just about heating and cooling—it’s about precise execution and consistency. Here are some key challenges faced by heat treating service providers:
1. Precision and Consistency
- Heat treating requires precise control over temperature and cooling rates.
- Even minor fluctuations can affect the strength and durability of the finished product.
- Manual monitoring increases the risk of inconsistency.
2. Equipment Maintenance and Downtime
- Heat treating equipment is complex and expensive.
- Unplanned downtime due to equipment failure can disrupt production and increase costs.
- Lack of predictive maintenance leads to higher repair costs and longer downtime.
3. Production Scheduling and Resource Allocation
- Managing multiple projects and work orders simultaneously can lead to scheduling conflicts.
- Inefficient use of resources increases production costs.
- Poor scheduling causes delays and reduces throughput.
4. Quality Control and Defect Tracking
- Maintaining consistent product quality is critical for customer satisfaction and regulatory compliance.
- Lack of real-time defect tracking increases scrap rates and production costs.
- Manual quality checks are time-consuming and prone to error.
5. Compliance and Reporting
- Heat treating services must comply with industry standards (e.g., ISO, ASTM) and safety regulations.
- Generating compliance reports manually is time-consuming and error-prone.
- Inaccurate reporting can result in fines and legal issues.
How ERP Solves These Challenges in Heat Treating Services
1. Precision Control and Automated Monitoring
ERP systems provide real-time monitoring and automated control over heat treating parameters, such as:
- Temperature, heating duration, and cooling rates.
- Material tracking and composition analysis.
- Batch processing with automated logging of process parameters.
✅ Example: A metal processing company reduced product defects by 25% after implementing an ERP system for real-time monitoring and automated control.
2. Predictive Maintenance and Equipment Management
ERP systems help prevent downtime by automating maintenance scheduling and equipment tracking:
- Track equipment performance and usage in real-time.
- Schedule maintenance based on predictive analytics.
- Receive automated alerts for potential issues before equipment failure.
✅ Example: A heat treating service provider reduced unplanned downtime by 30% using ERP-based predictive maintenance.
3. Streamlined Production Scheduling
ERP’s production scheduling tools enable heat treating companies to optimize resource allocation and meet deadlines more effectively:
- Real-time tracking of work orders and production status.
- Dynamic scheduling to adjust for changing workloads.
- Automatic resource allocation based on availability and order priority.
✅ Example: A manufacturing company increased production efficiency by 20% after adopting ERP-based scheduling.
4. Quality Control and Defect Tracking
ERP integrates quality control into the production process, allowing heat treating companies to:
- Set automated quality benchmarks.
- Track and resolve defects in real-time.
- Automate corrective actions to maintain consistency.
✅ Example: A heat treating plant reduced scrap rates by 15% after implementing automated defect tracking through ERP.
5. Regulatory Compliance and Reporting
ERP automates the generation of compliance reports and documentation:
- Track and store process data for easy auditability.
- Generate real-time compliance reports to meet industry standards.
- Automate safety checks and certifications.
✅ Example: A heat treating company cut compliance reporting time by 50% using ERP automation.
6. Real-Time Inventory and Material Management
ERP provides real-time visibility into raw material and finished product inventory:
- Track material consumption and reorder levels automatically.
- Manage multiple types of metals and treatment specifications.
- Reduce wastage and overstocking through automated inventory tracking.
✅ Example: A heat treating company reduced material costs by 18% through better inventory management.
7. Financial Oversight and Cost Control
ERP systems provide detailed cost analysis to help heat treating companies manage expenses:
- Track direct and indirect costs in real-time.
- Analyze profit margins for different treatment processes.
- Adjust pricing strategies based on cost analysis.
✅ Example: A heat treating firm improved profit margins by 12% after implementing ERP-based cost tracking.
8. Enhanced Customer Service and Order Tracking
ERP integrates customer service with production data to improve customer satisfaction:
- Provide real-time updates on order status.
- Track customer feedback and complaints.
- Automate order fulfillment and shipping tracking.
✅ Example: A heat treating company improved on-time delivery rates by 20% using ERP-based order tracking.
Benefits of Using ERP for Heat Treating Services
✔️ Increased production accuracy and consistency.
✔️ Reduced downtime and maintenance costs.
✔️ Improved inventory and material tracking.
✔️ Enhanced compliance and safety.
✔️ Better customer satisfaction through real-time order tracking.
✔️ Lower operational costs and higher profit margins.
Heat treating is a highly technical industry where precision and efficiency are critical. ERP systems offer heat treating services a powerful solution for automating processes, improving consistency, reducing costs, and enhancing customer satisfaction. From predictive maintenance and automated scheduling to real-time quality control and compliance tracking, ERP transforms how heat treating companies operate.
If your heat treating business is struggling with inefficiencies, inconsistent quality, or high operational costs, it’s time to explore how ERP can help. With ERP, you’ll stay in control—under pressure and beyond.
FAQs
1. How does ERP improve quality control in heat treating services?
ERP tracks production parameters and detects defects in real-time, ensuring consistent product quality.
2. Can ERP handle multi-location heat treating operations?
Yes, ERP allows centralized management of multiple heat treating plants and facilities.
3. How does ERP reduce equipment downtime in heat treating?
ERP uses predictive maintenance and real-time equipment monitoring to prevent unexpected failures.
4. Can ERP automate scheduling for heat treating processes?
Yes, ERP automates work order scheduling based on machine availability and order priority.
5. How does ERP help with compliance in heat treating services?
ERP automates the generation of compliance reports and monitors process data for audit trails.
6. Can ERP manage raw material inventory for heat treating?
Yes, ERP tracks raw material usage and automatically adjusts reorder levels based on demand.
7. How does ERP improve customer service in heat treating?
ERP provides real-time order status updates and automates order fulfillment processes.
8. Can ERP track heat treating costs and profitability?
Yes, ERP offers detailed cost analysis for each treatment process and helps adjust pricing strategies.
9. How does ERP handle complex heat treating specifications?
ERP allows customization of production parameters and creates unique work orders for each specification.
10. What industries benefit most from ERP in heat treating?
Industries like automotive, aerospace, metal fabrication, and construction benefit most from ERP in heat treating.
👉 Ready to heat up your operations with precision? Discover how ERP can transform your heat treating services today!