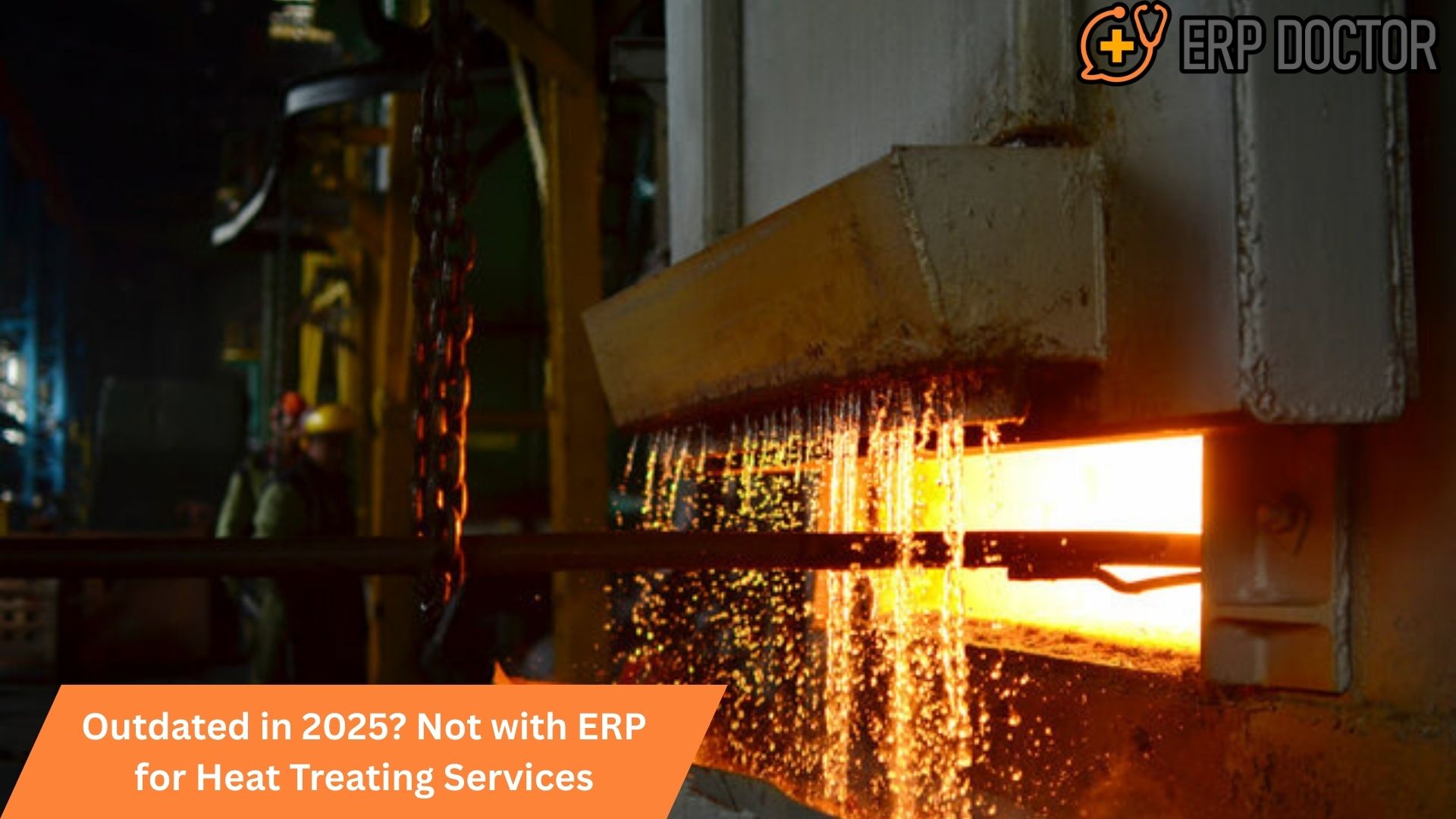
Outdated in 2025? Not with ERP for Heat Treating Services
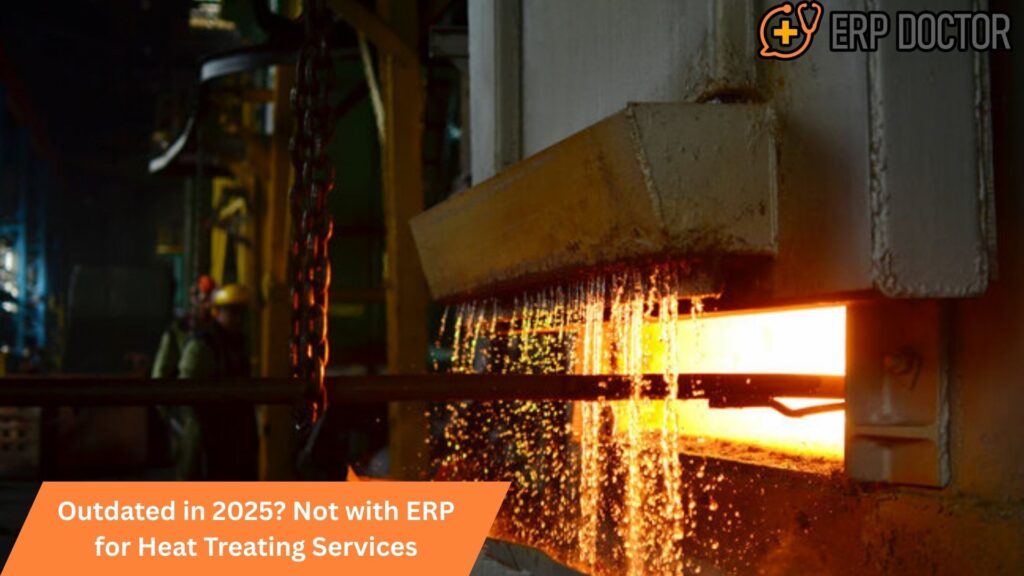
Why ERP Is Essential for Heat Treating Services in 2025
Introduction: The Pressure Is On
As we enter 2025, heat treating service providers face growing pressure from customers, regulatory bodies, and competitors. Whether it’s batch traceability, tight delivery schedules, or customer-specific specs, staying on top of operations is more critical than ever. But using outdated tools—like spreadsheets, manual logbooks, or disconnected software—won’t cut it anymore.
The solution? A modern ERP (Enterprise Resource Planning) system tailored for the heat treating service industry. It connects your processes, improves accuracy, and positions your company for sustainable growth.
What Is ERP and Why Does It Matter for Heat Treating?
An ERP system is software that manages all the core parts of a business—like scheduling, inventory, quality control, finance, and customer data—in one platform.
For a heat treating service provider, ERP goes beyond basic business management. It helps:
- Track each part or batch through the entire heat treating cycle
- Standardize work orders and reduce miscommunication
- Manage equipment usage, maintenance, and downtime
- Ensure compliance with industry standards
- Deliver precise reports for audits and customers
In short, ERP makes your heat treating service smarter, faster, and more competitive in 2025.
Outdated Systems Hurt More Than You Think
Still relying on manual logs or disconnected software?
Here’s what you risk:
- Production errors: Wrong temperatures or times due to poor tracking
- Missed deadlines: Lack of real-time job status updates
- Lost revenue: Inability to quote accurately or schedule efficiently
- Failed audits: Incomplete or inconsistent documentation
- Customer churn: Inconsistent service quality or lack of communication
An ERP system designed for heat treating services solves all of these pain points.
How ERP Benefits Heat Treating Services in 2025
🔹 1. Real-Time Job Tracking
Know where every part or order is in the heat treating process—from intake to delivery. ERP gives your team and customers full visibility.
🔹 2. Standardized Work Orders
Create digital, repeatable templates for every type of heat treating service. No more handwritten instructions or confusion.
🔹 3. Better Scheduling and Resource Planning
Optimize furnace loads, reduce idle time, and ensure your team works efficiently with ERP-powered production planning.
🔹 4. Quality Control and Compliance
Track temperatures, cycles, load times, and part data in real time. An ERP system makes passing audits easy by storing all certifications, test results, and compliance data.
🔹 5. Accurate Quoting and Invoicing
With real-time cost tracking and job history, ERP allows you to generate accurate quotes and invoices, reducing delays in payment and errors.
Why 2025 Is the Right Time to Upgrade
The heat treating service industry is evolving:
- Customers demand more transparency and digital updates
- Industry regulations are getting stricter
- Margins are tighter—efficiency is everything
- Skilled labor is harder to find—automation can bridge the gap
By implementing ERP in 2025, your heat treating service stays ahead of the curve instead of playing catch-up.
ERP Features Heat Treating Service Providers Should Look For
Not all ERP systems are created equal. If you’re in the heat treating service business, choose ERP software that includes:
- Job order tracking and part-level traceability
- Furnace and load planning tools
- Digital quality control records
- Maintenance and downtime logs
- Customer portals and job status notifications
- Reporting tools for NADCAP, ISO, or AS9100 compliance
These ERP features are designed to meet the real-world needs of heat treating operations in 2025 and beyond.
Case in Point: Real-World ROI with ERP
A mid-sized heat treating service company switched from manual scheduling to an ERP system. Within six months, they saw:
- 30% reduction in delayed orders
- 25% faster job scheduling and turnaround
- Zero non-compliance issues in their annual audit
- 40% improvement in customer satisfaction due to live job tracking
ERP wasn’t just a tech upgrade—it was a business transformation.
Integration Makes It Even Better
A modern ERP system integrates with:
- Barcode scanners for real-time tracking
- IoT sensors on furnaces
- Digital thermocouple readings
- Customer support tools and ticketing systems
- Accounting and payroll software
This means no more switching between systems—everything your heat treating service needs is under one digital roof.
Preparing Your Heat Treating Business for the Next 10 Years
ERP isn’t just about solving today’s problems—it’s about futureproofing. As your heat treating service grows, ERP systems scale with you:
- Add more furnaces, locations, or shifts
- Handle more customer jobs without adding admin overhead
- Expand into new certifications or industries
- Launch advanced analytics and performance monitoring
Investing in ERP now sets you up for a smarter, more sustainable decade of operations.
Final Thoughts: Don’t Be Left Behind in 2025
In 2025, running a heat treating service without ERP is like running a furnace without a thermostat—risky, inefficient, and outdated. With increasing customer demands and shrinking margins, efficiency, traceability, and automation are no longer optional—they’re essential.
ERP helps your heat treating service stay organized, grow faster, and deliver higher-quality results with fewer mistakes. If you want to stay competitive this year and beyond, now is the time to make the switch.
✅ FAQs
1. Why does the heat treating service industry need ERP in 2025?
ERP helps heat treating service companies improve efficiency, reduce manual errors, and meet growing customer and compliance demands in 2025.
2. How does ERP help with furnace load planning in heat treating services?
ERP optimizes furnace scheduling by analyzing job types, materials, and deadlines—ensuring faster, smarter resource usage.
3. Can ERP track part-level data in heat treating services?
Yes. ERP systems offer traceability by recording each part’s process cycle, temperature, and quality checks throughout the heat treating process.
4. What ERP features are best for heat treating service companies?
Look for job tracking, real-time monitoring, quality control logs, maintenance management, and customer communication tools.
5. Is ERP suitable for small or mid-sized heat treating businesses?
Absolutely. Many ERP solutions are scalable, making them perfect for small and mid-sized heat treating service providers.
6. How does ERP improve compliance in the heat treating industry?
ERP stores all required documentation for audits, including load charts, test results, and certifications, reducing the risk of non-compliance.
7. Can ERP help heat treating services reduce downtime?
Yes. ERP can schedule regular maintenance and monitor equipment performance, reducing unplanned downtime.
8. How fast can a heat treating service company implement ERP?
Implementation depends on complexity, but small to mid-sized heat treating services can go live in 3–6 months with the right support.
9. Does ERP integrate with sensors or thermocouple readers?
Yes. Many ERP systems integrate with IoT devices to track furnace temperatures and cycle performance in real time.
10. What is the ROI of ERP for heat treating services?
ERP delivers ROI through fewer errors, faster scheduling, better compliance, improved customer satisfaction, and lower operational costs.