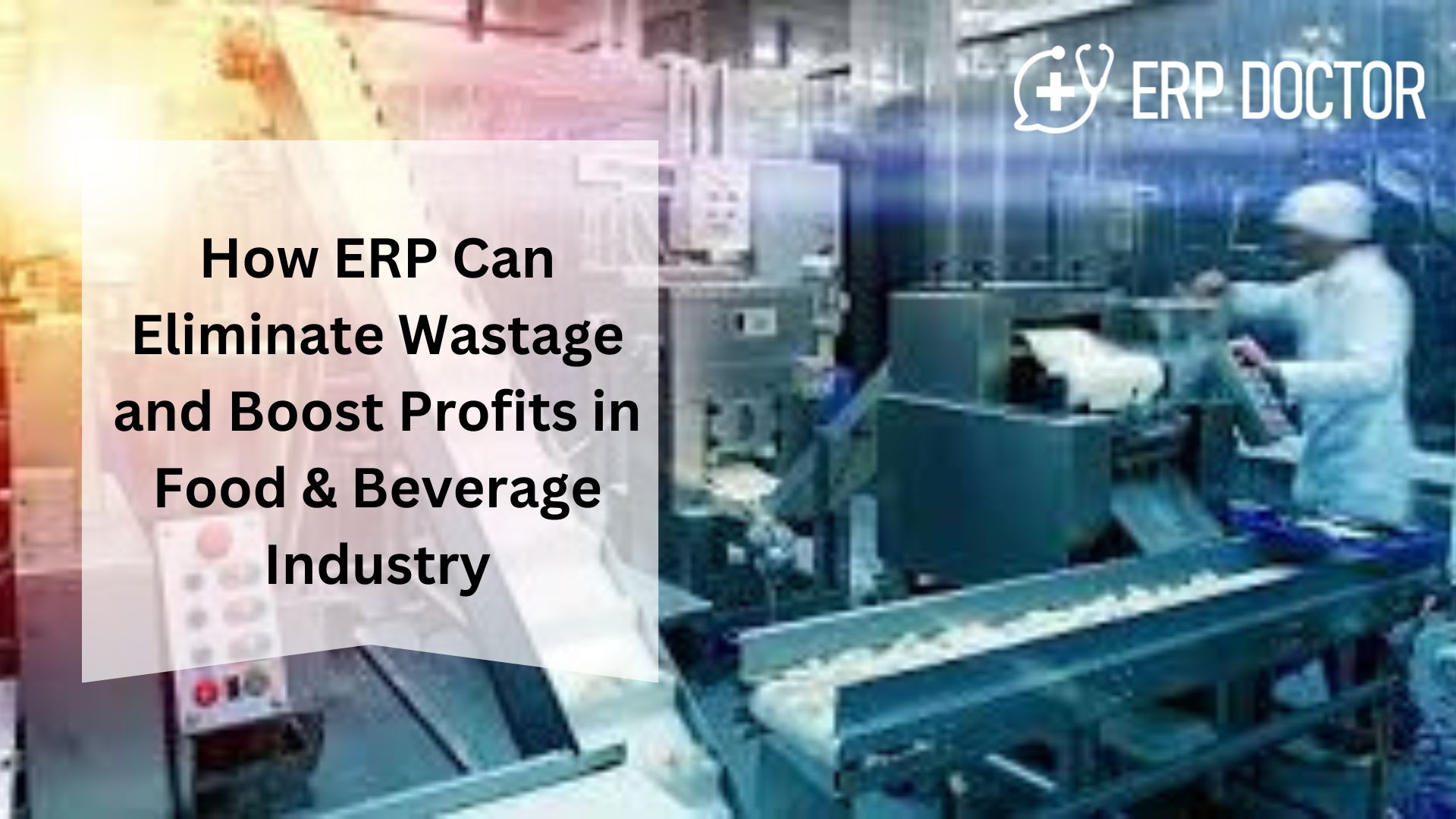
How ERP Can Eliminate Wastage and Boost Profits in Food & Beverage Industry
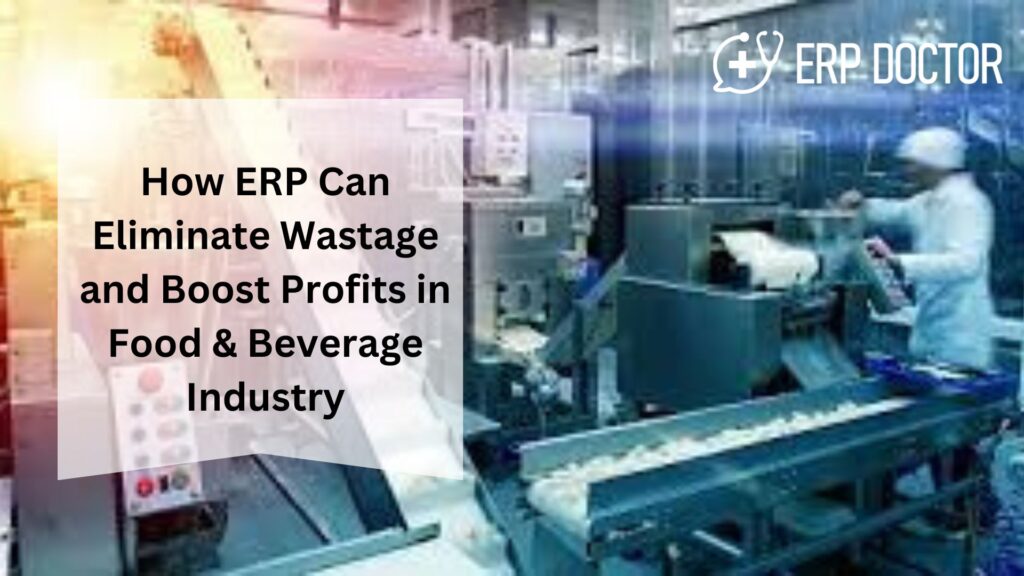
ERP in Food & Beverage: Key to Reducing Waste and Maximizing Profitability
The food and beverage industry faces unique challenges—ranging from inventory management to supply chain efficiency. As competition intensifies and margins tighten, businesses are turning to modern technologies to stay ahead. One such solution is Enterprise Resource Planning (ERP) software, which is transforming how companies in the food and beverage sector operate. By automating processes, streamlining supply chains, and improving visibility into business operations, ERP solutions for the food and beverage industry can play a pivotal role in eliminating wastage and boosting profits.
What Is ERP for the Food & Beverage Industry?
Enterprise Resource Planning (ERP) is a type of software that helps businesses integrate and manage core functions like finance, supply chain, production, inventory, and human resources. ERP for food & beverage industry is specially designed to address the specific needs of this sector, where perishable goods, regulations, and customer demand fluctuations are constant challenges.
By providing a unified platform for managing operations, ERP solutions for the food & beverage industry help businesses optimize resources, reduce waste, and improve operational efficiency.
1. Reducing Wastage in the Food & Beverage Industry
Wastage is a significant issue in the food and beverage industry. Spoiled inventory, overproduction, and inefficient supply chains can all contribute to unnecessary waste. ERP solutions can help companies manage these challenges by offering the following capabilities:
Real-Time Inventory Management
One of the main sources of wastage in the food industry is poor inventory control. With ERP for food & beverage businesses, companies can track inventory levels in real-time, ensuring that ingredients and products are used efficiently before they expire. By integrating sales data with inventory management, businesses can better predict demand, reorder stock on time, and avoid overstocking, all of which contribute to reducing waste.
Improved Forecasting and Demand Planning
Accurate demand forecasting is crucial for minimizing waste in the food and beverage industry. ERP systems analyze historical sales data, market trends, and external factors like seasonality to predict future demand more precisely. This enables businesses to produce or procure just the right amount of products, reducing overproduction and excess inventory that can lead to spoilage.
Waste Tracking and Reporting
ERP solutions allow businesses to track the reasons behind waste. Whether it’s food spoilage, production errors, or packaging problems, businesses can identify the root causes and take corrective actions. Detailed waste reporting also helps identify inefficiencies in the production process, allowing companies to fine-tune operations and reduce waste over time.
2. Enhancing Supply Chain Efficiency
An optimized supply chain is essential for the food and beverage industry. Delays, disruptions, or inefficiencies can lead to missed opportunities and increased wastage. ERP software helps streamline supply chain management in several ways:
Real-Time Supply Chain Visibility
With ERP, food and beverage companies can gain end-to-end visibility into their supply chain. From raw material procurement to finished goods delivery, businesses can monitor the flow of products and make adjustments on the fly. This helps avoid stockouts, excess inventory, and bottlenecks that can lead to wastage.
Supplier and Vendor Management
A strong relationship with suppliers and vendors is vital to ensure the timely and quality delivery of ingredients and materials. ERP solutions for food & beverage businesses facilitate efficient communication and performance tracking with suppliers. Businesses can track delivery times, quality standards, and pricing, ensuring that they receive the right materials at the right time—reducing delays and potential wastage.
Compliance with Regulations
Food safety and quality regulations are stringent in the food and beverage industry. ERP systems help businesses maintain compliance with industry standards, such as HACCP (Hazard Analysis and Critical Control Points), by offering tools to track batch numbers, expiration dates, and traceability. By ensuring product quality and compliance, businesses can minimize the risk of recalls and wasted goods due to non-compliance.
3. Improving Production Efficiency
Efficient production is key to minimizing costs and boosting profitability in the food and beverage sector. ERP solutions optimize the production process by offering the following features:
Automated Workflows
ERP systems automate routine tasks such as scheduling, production planning, and order processing. This reduces human error, speeds up production cycles, and ensures that resources are used efficiently. By eliminating bottlenecks and reducing downtime, businesses can improve overall production efficiency, which can directly translate to cost savings and reduced waste.
Optimal Resource Allocation
ERP solutions enable food and beverage businesses to allocate resources—such as labor, equipment, and raw materials—more efficiently. With precise tracking of production capacity, ERP software helps companies avoid overproduction or underutilization of resources, leading to fewer inefficiencies and less waste.
Product Lifecycle Management
ERP software helps food and beverage companies track the entire lifecycle of products, from raw materials to the final product. By understanding each phase of production, businesses can identify areas where waste is occurring and implement process improvements to reduce inefficiencies.
4. Boosting Profits Through Operational Efficiency
By eliminating wastage and improving operational processes, ERP software directly contributes to boosting profits in the food and beverage industry. Some key profit-boosting benefits include:
Cost Savings
Reducing waste, improving production efficiency, and optimizing supply chain management all contribute to lowering operational costs. Businesses can use ERP data to identify areas for cost-cutting, such as optimizing inventory levels, improving procurement practices, and automating administrative tasks.
Enhanced Decision-Making
ERP systems provide real-time data and insights that empower managers to make better, more informed decisions. Whether it’s adjusting production schedules based on demand forecasts or negotiating better supplier contracts, the data provided by ERP software can help businesses optimize their operations and increase profitability.
Scalable Growth
As businesses in the food and beverage industry grow, ERP solutions can scale to meet increasing demands. With advanced reporting and analytics, ERP systems help businesses identify new opportunities for growth, whether through expanding into new markets, offering new products, or improving operational efficiency.
In today’s competitive food and beverage industry, reducing waste and optimizing operations are critical to maintaining profitability. ERP for food & beverage businesses offers comprehensive solutions that address the sector’s unique challenges, from inventory management to supply chain efficiency and production optimization. By eliminating wastage, improving operational efficiency, and enabling better decision-making, ERP solutions for the food & beverage industry are essential tools for boosting profits and ensuring long-term success.
Adopting ERP technology isn’t just about reducing waste—it’s about future-proofing your business in a fast-paced and ever-evolving industry. With the right ERP system in place, food and beverage businesses can not only survive but thrive in a competitive market.
FAQ – ERP for Food & Beverage
1. What is ERP for the food and beverage industry?
ERP (Enterprise Resource Planning) for the food and beverage industry is specialized software that helps businesses manage various functions such as inventory, production, supply chain, and compliance in a single system. It helps streamline operations, reduce waste, and improve efficiency.
2. How does ERP reduce waste in the food and beverage sector?
ERP helps reduce waste by providing real-time inventory tracking, improving demand forecasting, and optimizing production schedules. This ensures businesses only produce or stock what is needed, minimizing spoilage and overproduction.
3. Can ERP improve supply chain management in the food and beverage industry?
Yes, ERP improves supply chain management by providing real-time visibility into inventory and supplier performance. This helps businesses manage deliveries, avoid delays, and ensure they receive the right materials on time, reducing waste and inefficiencies.
4. How does ERP help in boosting profits for food and beverage companies?
ERP boosts profits by cutting costs associated with waste, production inefficiencies, and inventory mismanagement. It also helps companies make data-driven decisions, optimize resources, and improve operational efficiency, leading to better profit margins.
5. What are the key benefits of ERP solutions for the food and beverage industry?
Key benefits of ERP in the food and beverage industry include reduced waste, improved inventory and production management, better demand forecasting, compliance with industry regulations, and enhanced decision-making—all of which contribute to increased profitability.
Visit ERP Doctor for Expert Solutions and Support
Want to speak to an expert? Fill in the form below, and we will be in touch with you shortly!