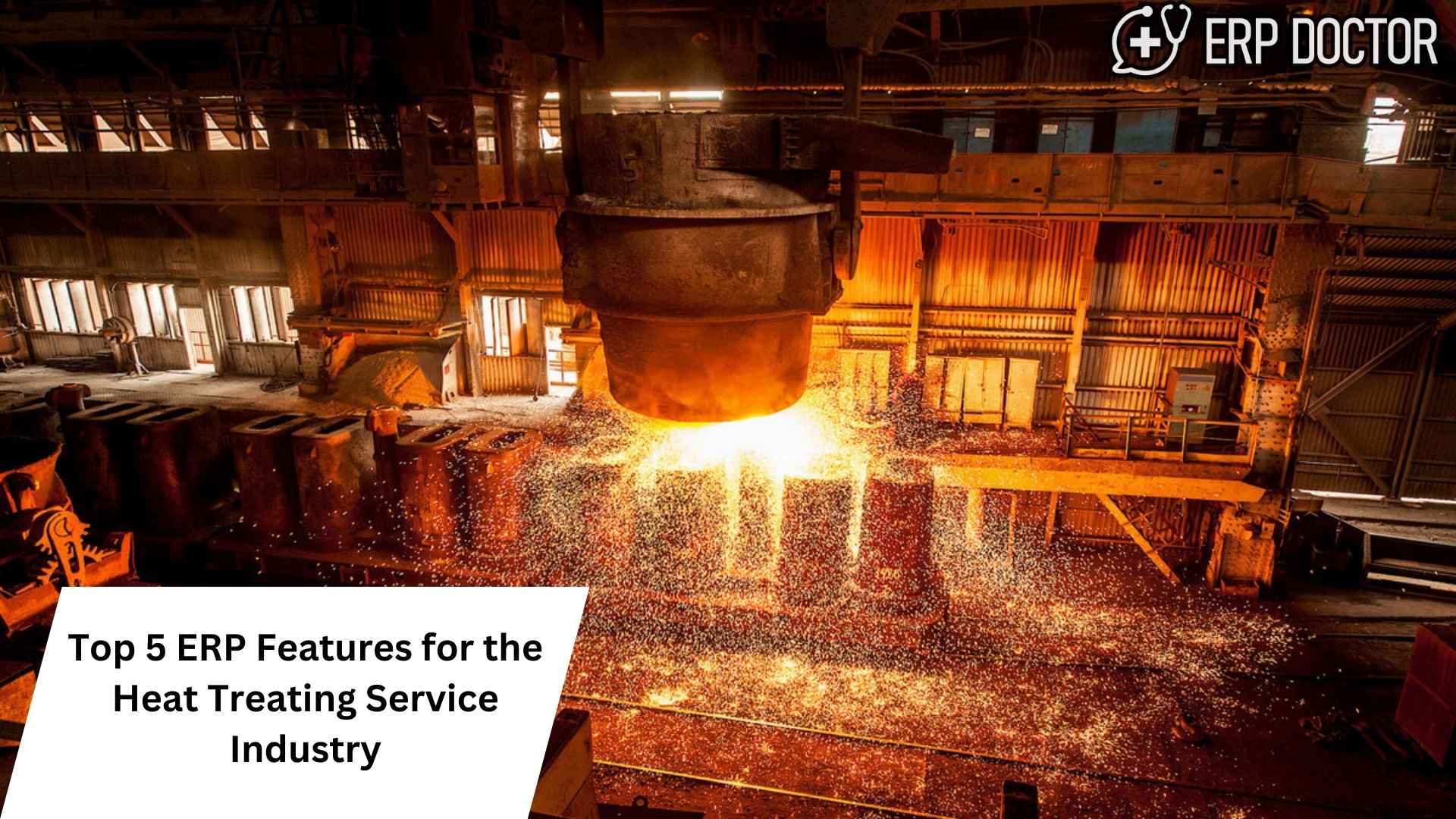
ERP for the Heat Treating Service Industry: Proven Success Guide
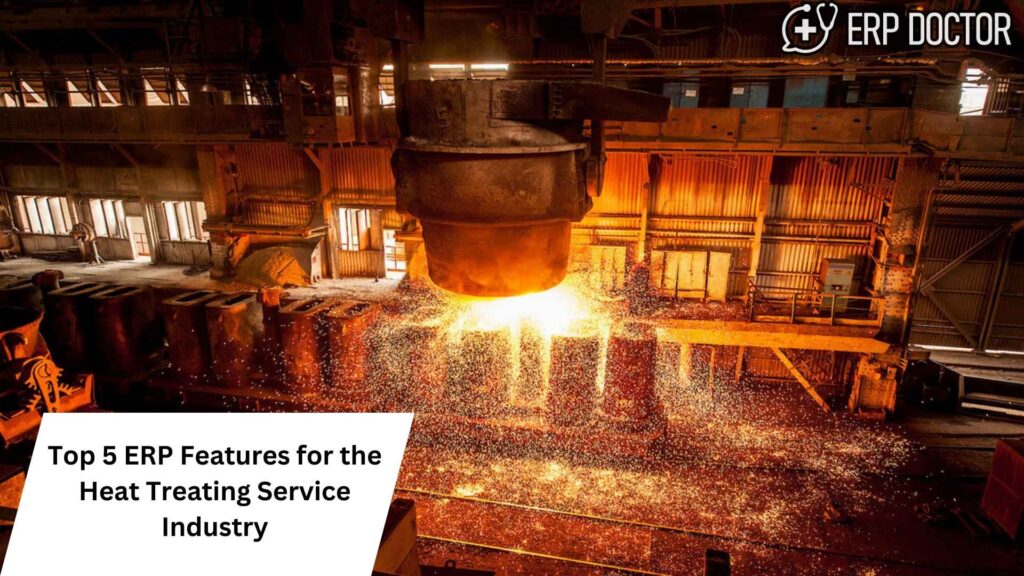
ERP for the Heat Treating Service Industry: 5 Game-Changing Features You Need to Succeed
The Heat Treating Service Industry plays a vital role in manufacturing, ensuring materials achieve optimal durability, strength, and performance. However, managing complex processes, maintaining strict compliance, and ensuring operational efficiency can be challenging. ERP (Enterprise Resource Planning) systems provide a comprehensive solution, streamlining workflows and improving productivity. In this blog, we will explore the top 5 ERP features for the Heat Treating Service Industry that enhance efficiency and compliance.
1. Advanced Production Planning & Scheduling
Production in the Heat Treating Service Industry requires precise scheduling to ensure efficiency and avoid bottlenecks. An ERP system automates scheduling, allocates resources efficiently, and minimizes downtime. With real-time visibility, businesses can manage workload distribution effectively, ensuring optimal furnace utilization.
2. Quality Control & Compliance Management
Quality assurance is a top priority in the Heat Treating Service Industry. ERP solutions integrate automated quality checks, real-time tracking, and documentation to meet stringent industry regulations. Features such as audit trails, compliance tracking, and defect analysis help companies meet ISO and ASTM standards while maintaining customer trust.
3. Inventory & Material Management
Effective material tracking is crucial for maintaining stock levels and reducing waste in the Heat Treating Service Industry. An ERP system optimizes raw material procurement, tracks inventory in real-time, and ensures just-in-time (JIT) stock replenishment. This reduces excess inventory costs while preventing shortages that may disrupt production.
4. Real-time Data & Reporting
To maintain efficiency and profitability, businesses in the Heat Treating Service Industry need real-time insights into operations. ERP systems offer dynamic dashboards, KPI tracking, and automated reporting tools, allowing decision-makers to analyze performance, identify inefficiencies, and optimize processes for better outcomes.
5. Equipment Maintenance & Lifecycle Management
Unplanned equipment failures can lead to costly downtime in the Heat Treating Service Industry. An ERP system helps track maintenance schedules, monitor equipment health, and automate preventive maintenance tasks. This ensures smooth operations, extends equipment lifespan, and prevents unexpected breakdowns that can halt production.
Implementing ERP solutions in the Heat Treating Service Industry significantly enhances productivity, compliance, and profitability. By leveraging ERP features such as production planning, quality control, inventory management, real-time reporting, and equipment maintenance, companies can achieve streamlined operations and sustainable growth.
FAQs
1. How does ERP help in the Heat Treating Service Industry?
ERP automates production planning, ensures quality compliance, optimizes inventory, and streamlines overall operations, enhancing efficiency.
2. Can ERP systems manage multiple heat treatment processes?
Yes, ERP solutions support various heat treatment processes, including annealing, quenching, tempering, and carburizing, ensuring seamless operations.
3. What compliance standards does ERP help meet in the Heat Treating Service Industry?
ERP systems assist in meeting industry standards such as ISO, ASTM, and NADCAP by automating documentation and audit trails.
4. How does ERP improve equipment maintenance in the Heat Treating Service Industry?
ERP tracks maintenance schedules, automates servicing alerts, and monitors equipment health to prevent unexpected breakdowns.
5. Does ERP optimize inventory in the Heat Treating Service Industry?
Yes, ERP provides real-time inventory tracking, prevents overstocking, and ensures just-in-time (JIT) material procurement.
6. Can small-scale heat treatment businesses benefit from ERP?
Absolutely! ERP solutions are scalable and can be tailored to fit the needs of small, medium, and large heat treatment businesses.
7. How does ERP assist in workforce management?
ERP streamlines workforce allocation, automates payroll management, and ensures employees are assigned efficiently based on skill sets.
8. What role does ERP play in customer order tracking?
ERP provides real-time tracking of customer orders, enhances communication, and ensures timely deliveries.
9. How does ERP enhance data security in the Heat Treating Service Industry?
ERP systems offer robust data encryption, role-based access control, and secure cloud storage for sensitive operational data.
10. What is the ROI of implementing ERP in the Heat Treating Service Industry?
By reducing downtime, optimizing resource usage, and improving operational efficiency, ERP delivers a high return on investment (ROI) over time.
By integrating ERP into the Heat Treating Service Industry, businesses can achieve operational excellence, ensure regulatory compliance, and drive long-term success.