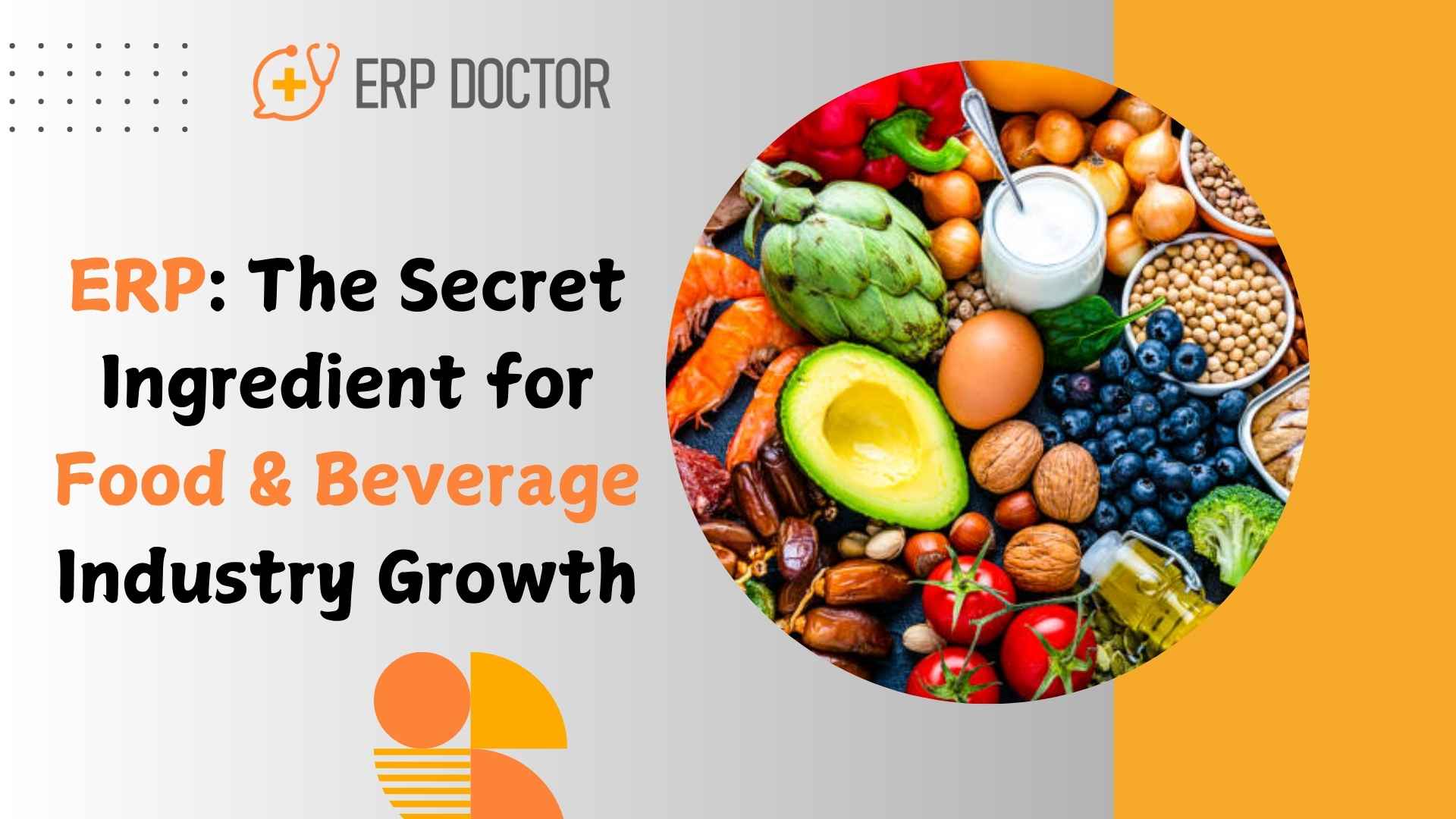
ERP: The Secret Ingredient for Food & Beverage Industry Growth
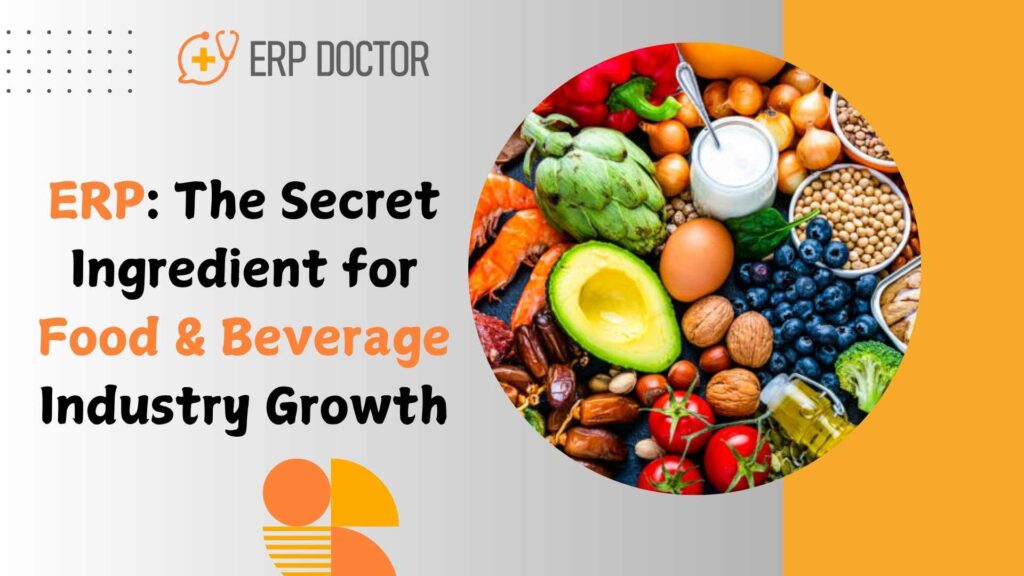
Serving Up Efficiency with ERP in Food and Beverage
The food and beverage (F&B) industry is a complex and competitive arena. From navigating intricate supply chains and adhering to stringent regulations to meeting ever-evolving consumer demands, Food and Beverage businesses face unique challenges. In this dynamic environment, Enterprise Resource Planning (ERP) systems have emerged as a critical tool, offering a potent blend of functionalities that can fuel growth and success. This blog post explores how ERP acts as the secret ingredient for Food and Beverage industry growth, examining its key benefits and addressing common concerns.
Navigating the F&B Maze: Key Challenges
F&B businesses operate within a complex ecosystem, facing a range of interconnected challenges:
- Supply Chain Complexity: Managing a global network of suppliers, dealing with fluctuating raw material prices, and handling perishable goods require sophisticated coordination.
- Regulatory Scrutiny: Stringent food safety and labeling regulations (like HACCP and FSMA) demand meticulous compliance.
- Traceability Imperative: Rapid and accurate product tracing is crucial for managing recalls and safeguarding consumer trust.
- Perishable Goods Management: Minimizing waste and spoilage of perishable items demands precise inventory control and efficient logistics.
- Seasonal Demand Swings: Meeting seasonal demand peaks and troughs necessitates flexible production planning and agile inventory management.
- Quality Assurance: Maintaining consistent product quality is paramount for brand reputation and customer loyalty.
ERP in Food and Beverage: A Recipe for Success
ERP systems offer a comprehensive suite of tools designed to address these specific challenges:
- Streamlined Supply Chain: ERP provides end-to-end visibility into the supply chain, from procurement and inventory management to warehouse operations and logistics. Real-time data empowers businesses to optimize purchasing, reduce lead times, and minimize stockouts.
- Optimized Production: ERP facilitates production planning, scheduling, and execution, maximizing resource utilization and ensuring timely delivery. It supports recipe management, batch tracking, and quality control throughout the production lifecycle.
- Enhanced Quality and Compliance: ERP integrates quality checks at every stage of production, tracks defects, and manages corrective actions. It also assists with generating compliance reports and adhering to industry regulations.
- Robust Traceability: ERP enables comprehensive product tracing, from raw materials to finished goods. This capability is essential for managing recalls effectively and protecting consumers.
- Efficient Inventory Management: Real-time inventory visibility allows businesses to optimize stock levels, reduce waste, and prevent stockouts. ERP also facilitates inventory valuation, tracking, and reporting.
- Integrated Financial Management: ERP automates financial processes, including accounting, payables/receivables, and financial reporting, improving accuracy and providing real-time financial insights.
- Improved Sales and Distribution: ERP streamlines order processing, manages customer relationships, and optimizes distribution logistics, leading to enhanced customer service and increased sales performance.
Taste of Success: Benefits of ERP in Food and Beverage
Implementing ERP in the F&B industry yields a range of tangible benefits:
- Increased Efficiency: Automation of manual processes frees up valuable time and resources.
- Reduced Costs: Streamlined operations and optimized resource allocation lead to significant cost savings.
- Improved Traceability: Enhanced traceability minimizes the impact of recalls and strengthens consumer trust.
- Optimized Inventory: Efficient inventory management reduces waste and maximizes profitability.
- Enhanced Quality: Integrated quality control measures ensure consistent product quality.
- Strengthened Compliance: ERP facilitates adherence to industry regulations, minimizing risk.
- Better Decision-Making: Real-time data insights empower informed and timely decision-making.
- Increased Profitability: Improved efficiency, reduced costs, and enhanced decision-making drive profitability.
Choosing the Right ERP Partner
Selecting the right ERP system is crucial for a successful implementation. Consider these key factors:
- F&B Industry Expertise: Choose a system specifically designed for the nuances of the F&B industry.
- Scalability: Ensure the system can grow with your business.
- Integration Capabilities: Verify seamless integration with existing systems.
- Vendor Reputation and Support: Select a reputable vendor with robust support and training programs.
- Total Cost of Ownership (TCO): Carefully evaluate all costs, including software, implementation, training, and maintenance.
Conclusion: ERP as a Catalyst for Growth
In the competitive Food and Beverage landscape, ERP systems are no longer a luxury but a necessity. They provide a powerful platform for optimizing operations, enhancing efficiency, and driving sustainable growth. By carefully considering their needs and selecting the right ERP solution, F&B businesses can unlock their full potential and achieve lasting success.
FAQs for Food and Beverage in ERP
What is the typical ROI of an ERP implementation in the F&B industry?
ROI varies, but common benefits include reduced inventory costs, improved production efficiency, and increased sales.
How long does it take to implement an ERP system?
Implementation timelines vary, typically ranging from several months to a year.
What are key considerations when choosing an ERP vendor for F&B?
Look for F&B industry experience, strong references, and robust support.
How does ERP help manage traceability and recalls?
ERP enables end-to-end product tracing, crucial for effective recall management.
What is the role of cloud computing in F&B ERP?
Cloud-based ERP offers flexibility, scalability, and cost-effectiveness.
How does ERP aid compliance with food safety regulations?
ERP tracks requirements, generates reports, and ensures adherence to standards like HACCP.
What are the challenges of global F&B supply chain ERP implementation?
Managing multiple currencies, languages, and regulations requires a robust global ERP solution.
How can F&B companies leverage data analytics in ERP?
Data analytics provides insights into sales trends, inventory levels, and production efficiency.
Why is change management important in ERP implementations?
Change management ensures a smooth transition and user adoption of the new system.
How can I measure the success of an ERP implementation?
Track KPIs like inventory turnover, order fulfillment rates, and production efficiency.
Looking for the right ERP solution for your Food and Beverage business? Contact us today!