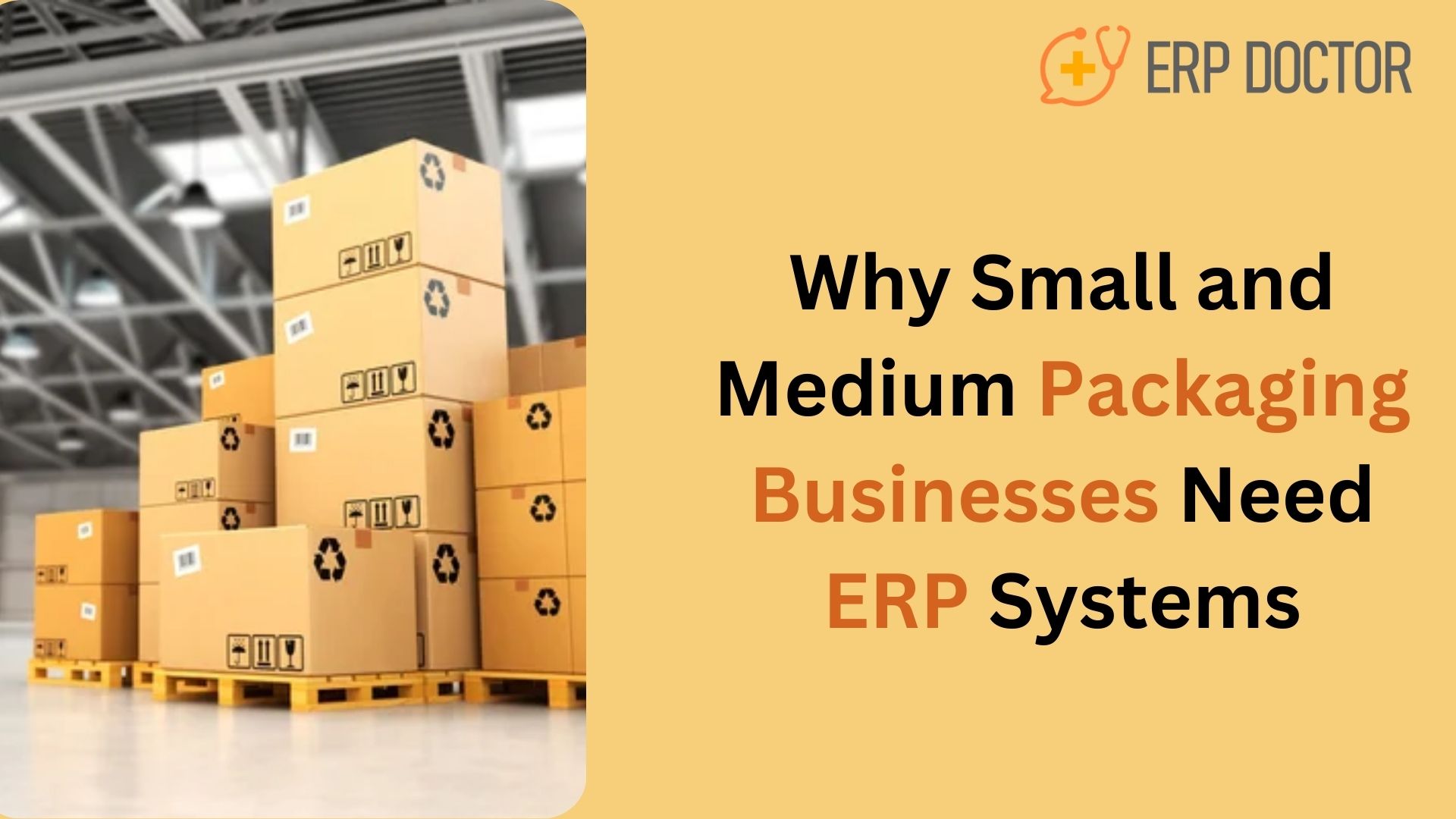
Why Small and Medium Packaging Businesses Need ERP Systems
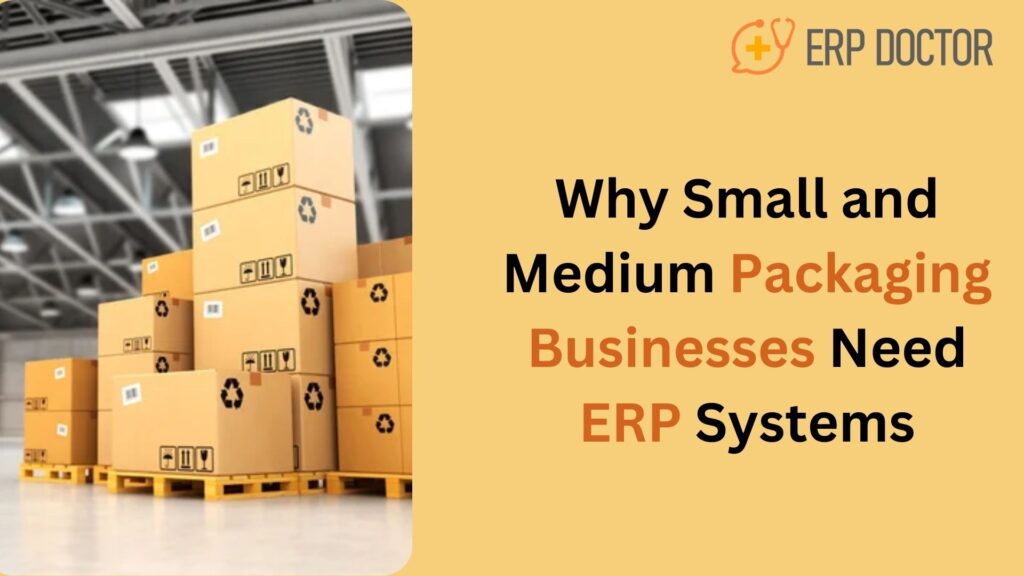
The ERP Advantage: Empowering Packaging SMBs to Succeed
In the fast-paced and competitive world of the packaging industry, small and medium businesses (SMBs) often struggle with unique challenges. These include managing complex supply chains, fluctuating demand, inventory control, and ensuring quality—all while keeping costs low. An Enterprise Resource Planning (ERP) system offers a powerful solution, enabling SMBs in the packaging industry to streamline operations, enhance productivity, and gain a competitive edge. This blog delves into why ERP systems are crucial for SMBs in the packaging sector, how they address industry pain points, and the transformative benefits they bring.
SMB Packaging Industry Challenges: Identifying Solutions
Inventory Management: SMBs often lack the resources to effectively manage raw materials, semi-finished goods, and finished products. This can lead to overstocking or stockouts, directly impacting profitability.
Inefficient Workflow and Processes: Manual processes and disconnected systems hinder operational efficiency, causing delays and errors.
Regulatory Compliance: Packaging businesses must adhere to various local and international regulations, which can be difficult to track and manage manually.
Limited Scalability: As SMBs grow, their current systems may fail to support increasing operational complexity.
Cost Pressures: Rising material costs and thin profit margins necessitate operational efficiency to stay competitive.
How ERP Systems Solve These Challenges
An ERP system integrates all business processes into a single platform, providing real-time data, automation, and control. Here’s how it specifically helps SMBs in the packaging industry:
Improved Inventory Management: ERP systems offer advanced inventory tracking capabilities, helping SMBs monitor stock levels, predict demand, and minimize waste. Features like just-in-time (JIT) inventory ensure optimal stock availability without overburdening storage capacity.
Enhanced Workflow Efficiency: By automating tasks like order processing, production scheduling, and quality checks, ERP eliminates manual errors and speeds up operations. This ensures smooth workflows and timely delivery.
Regulatory Compliance: An ERP system keeps SMBs updated with industry regulations, automating compliance reporting and ensuring adherence to packaging standards such as labeling and environmental sustainability.
Scalability for Growth: ERP systems are scalable, enabling businesses to add modules or users as they grow. This ensures that SMBs can adapt to increasing demands without overhauling their systems.
Cost Reduction: ERP helps minimize operational costs through better resource utilization, process optimization, and reduced material wastage.
Data-Driven Decision-Making: Real-time analytics and reporting provide SMBs with insights into operational performance, helping them make informed decisions and identify growth opportunities.
Benefits of ERP for Small and Medium Packaging Businesses
Centralized Operations: ERP integrates all functions—production, sales, inventory, and finance—into one platform, offering a unified view of operations.
Increased Productivity: Automation of repetitive tasks allows employees to focus on strategic activities, boosting overall productivity.
Enhanced Customer Satisfaction: With better order tracking and timely delivery, businesses can improve customer satisfaction and build long-term relationships.
Better Resource Allocation: ERP systems optimize the use of labor, machinery, and materials, ensuring resources are allocated efficiently.
Competitive Advantage: By enabling SMBs to operate like larger enterprises, ERP provides the tools needed to compete in the global marketplace.
Key Features to Look for in an ERP System for Packaging SMBs
- Production Management
Real-time monitoring of production schedules, machine performance, and output quality. - Inventory and Supply Chain Management
Tools for tracking inventory levels, managing suppliers, and optimizing logistics. - Regulatory Compliance Tools
Built-in features for tracking and reporting compliance requirements. - Scalability and Flexibility
The ability to scale operations and customize modules based on business needs. - User-Friendly Interface
An intuitive interface ensures easy adoption and minimal training for employees.
Steps to Implement ERP in a Packaging Business
- Needs Assessment
Identify business challenges and determine the specific ERP features required. - Choose the Right ERP Vendor
Select a vendor with experience in the packaging industry and robust customer support. - Plan for Integration
Ensure the ERP system integrates seamlessly with existing tools and processes. - Employee Training
Train employees to use the ERP system effectively, addressing any resistance to change. - Monitor and Optimize
Continuously monitor system performance and make adjustments as needed.
FAQ: ERP for Small and Medium Packaging Businesses
1. How does an ERP system improve the customization of packaging solutions?
ERP systems allow businesses to store detailed customer preferences, manage design templates, and streamline production planning, enabling faster and more efficient delivery of customized packaging solutions.
2. Can an ERP system help with eco-friendly packaging initiatives?
Yes, ERP systems can track the usage of sustainable materials, monitor waste reduction efforts, and ensure compliance with environmental standards, helping SMBs achieve eco-friendly goals.
3. Is ERP suitable for SMBs with limited technical expertise?
Modern ERP systems are designed with user-friendly interfaces and minimal training requirements, making them accessible even for businesses with limited technical expertise.
4. How does ERP support seasonal demand in the packaging industry?
ERP systems provide demand forecasting tools and inventory optimization features that help SMBs prepare for seasonal fluctuations without overstocking or missing deadlines.
5. Will an ERP system disrupt ongoing packaging operations during implementation?
While ERP implementation may involve some initial adjustments, phased rollouts and proper planning can minimize disruptions, ensuring operations continue smoothly.
6. Can ERP help with real-time tracking of packaging orders?
Absolutely! ERP systems provide real-time updates on order statuses, enabling SMBs to offer accurate delivery timelines and enhance customer satisfaction.
7. How does an ERP system ensure quality control in packaging?
ERP systems include quality management modules that monitor production processes, automate defect detection, and ensure adherence to quality standards.
8. Is ERP useful for managing packaging designs and specifications?
Yes, ERP can centralize design data, track version control, and ensure consistent specifications are followed across production batches.
9. How does ERP address compliance for packaging exports?
ERP systems automate documentation for export compliance, ensuring packaging materials and processes meet international standards and regulations.
10. What role does ERP play in cost estimation for packaging projects?
ERP provides tools for accurate cost estimation by analyzing material costs, labor requirements, and production timelines, helping SMBs maintain profitability.
Empowering Sustainable Growth in Packaging SMBs
For small and medium packaging businesses, adopting an ERP system is no longer a luxury—it’s a necessity. By streamlining operations, improving efficiency, and enabling data-driven decision-making, ERP systems empower SMBs to overcome industry challenges and achieve sustainable growth.
If your packaging business is ready to take the leap, explore ERP solutions tailored to your needs today!