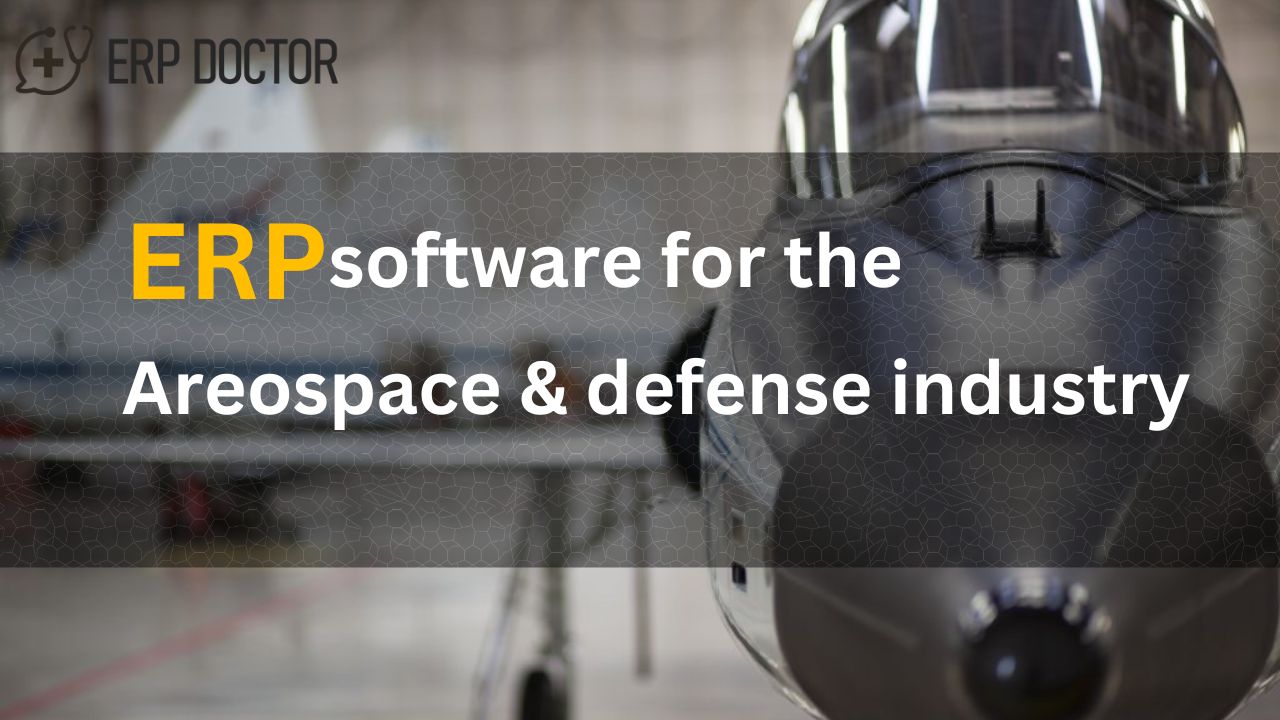
ERP Software for the Aerospace & Defense Industry
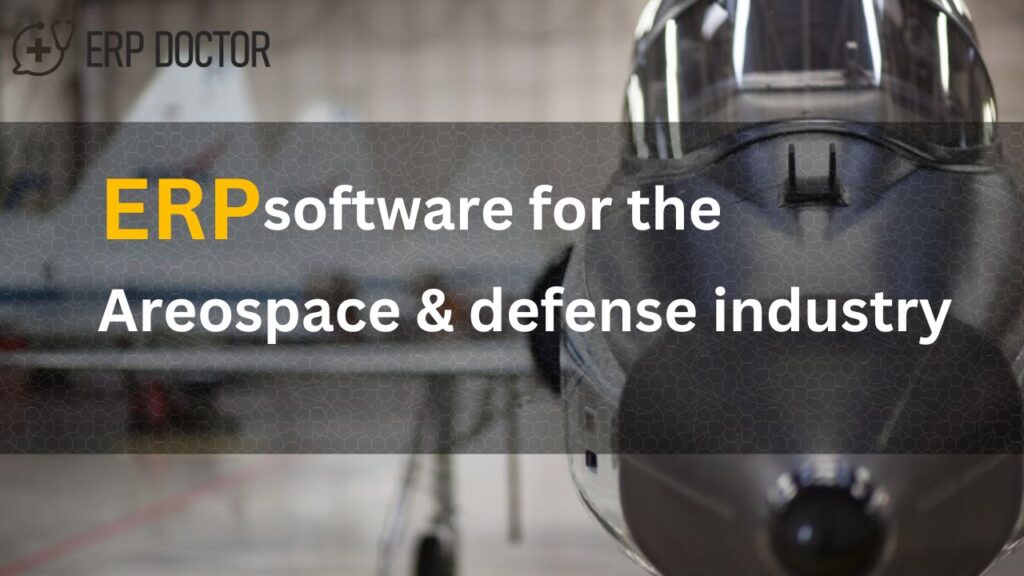
Elevating Efficiency: ERP Software Designed for the Aerospace & Defense Sector
ERP, particularly tailored for the Aerospace & Defense sector, facilitates the management of intricate supply chains, ensures adherence to regulatory standards, streamlines production processes, and enhances project management capabilities. In this sector, suppliers of parts and logistics face the critical task of meticulously complying with rigorous standards, navigating complex global supply networks, meeting demanding delivery schedules, and operating in a sales environment characterized by skepticism. Given the industry’s complexity and competitiveness, strict compliance with regulations is imperative. Any failure to meet these standards could lead to significant consequences, negatively impacting supply chain efficiency, vendor relationships, and overall profitability.
Vertical
Precision CNC Milling & Turning, 3 & 4 Axis Machined Components for Aerospace Applications, and Molding, as well as Tools & Fixtures for other Industrial Applications.
Order to Cash
The entire process from Order Management to Credit Management, Order Fulfillment, Order Shipping, AR Customer Invoicing, I/P, and Report generation is efficiently managed through ERP.
Procure to Pay
By integrating SAP B1 ERP, purchasing and accounts payable systems can be easily managed with efficiency. The MRP wizard automatically generates Purchase Requests based on Bill of Materials (BOM), which are then converted into Purchase Orders. Goods receipt is handled by stores, leading to Accounts Payable invoices and Outgoing payments.
Sales Order
Sales Orders in SAP B1 ERP for Aerospace & Defense are created upon PO generation or confirmation of Quotations by customers. SAP B1 ERP automatically populates fields such as Payment Terms and Delivery Dates from customer master data, with Committed Limit Management ensuring control.
Sales Quote
ERP streamlines the creation of Sales Quotations, automatically populating relevant fields and emailing PDFs directly to customers.
MRP
ERP’s Material Requirements Planning (MRP) functionality facilitates efficient planning and production processes, automatically generating Production Orders and Purchase Requests.
Purchase Request
Material Requirements Planning in ERP automatically generates Purchase Requests. Additionally, departments can manually create PRs for office equipment, consumables, etc., against which Purchase Orders are generated.
Purchase Order
Purchase Orders are created through approval procedures in ERP, with PDFs directly emailed to vendors.
Goods Receipt PO (GRPO)
Upon delivery from vendors, Goods Receipt against Purchase Orders is posted in ERP, updating inventory and enabling seamless Accounts Payable processes.
Supplier Payment
Supplier payments are initiated based on Goods Receipt in ERP, with AP invoices being matched against outgoing payments.
Production
ERP supports production processes by automatically generating Production Orders based on the Bill of Materials and demand. Additionally, it facilitates the issuance of Raw Materials and the receipt of Finished Goods, along with reporting completion of production orders.
Invoicing
ERP streamlines the creation of both Account Payable and Account Receivable invoices, ensuring accurate and timely payment entries.
Service
Facility management is efficiently handled through ERP’s software service module.
To learn more about our services, do visit us at:https://erpdoctor.in/